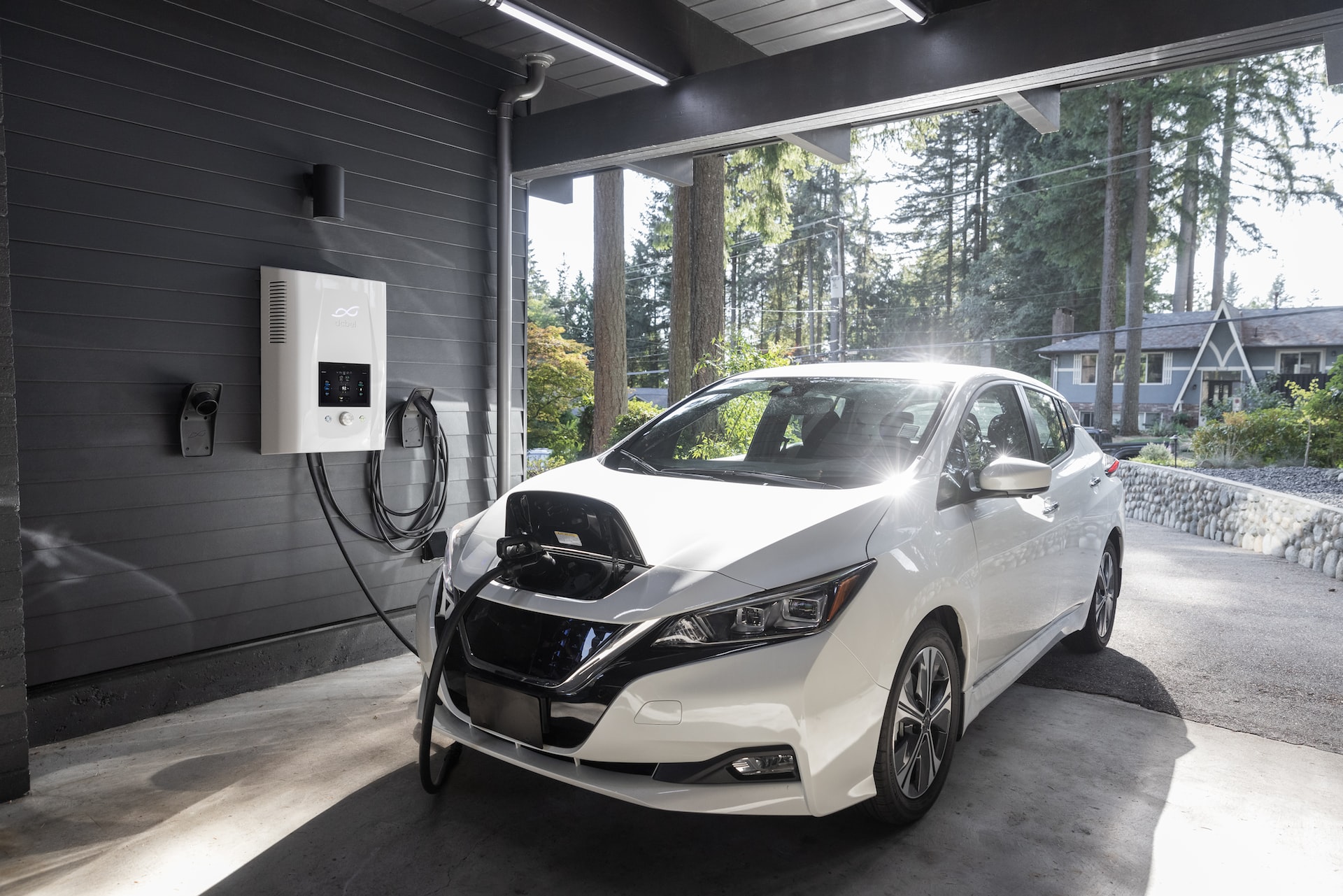
EV industry growth is expected to continue
Let's find out what are the future trends regarding producing EV cars.
Heading 2
Heading 3
Heading 4
Heading 5
Heading 6
Heading
KEY POINTS
- Electric vehicle ("EV") production and usage have increased dramatically over the past decade, with growth expected to continue into the next few decades.
One of the main costs of EVs is the EV battery. - Battery chemistry requires large amounts of lithium, nickel, and graphite.
- Demand for lithium, nickel, and graphite will rise significantly. That will require new sources of minerals to be discovered, developed, and financed before they can go into production.
ESG and supply chain factors are also driving the EV industry to identify new local sources of supply of such critical minerals.
Growth of EV sector? Is it real?
The growth in production of electric vehicles (“EV”) is dramatic as per the following graph which shows the growth sales of EVs globally over the past few years split by region:
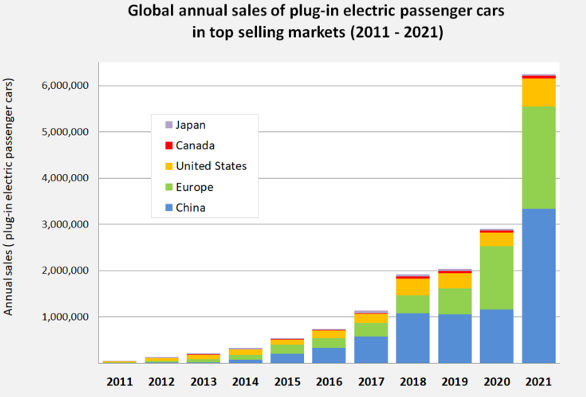
This growth trend is expected to continue and therefore will drive the demand for more supply of EV batteries (“EVB”) which require significant amounts of specific minerals for manufacture and all of these require some form of mining to supply the EVB manufacturers their required raw materials.
What are EV batteries?
An EVB is a rechargeable battery used to power the electric motors of EVs. Usually, these are lithium-ion batteries, which are designed for high electric charge (or energy) capacity at a given weight. The ability to have as small and light a battery as possible is important for EV efficiency. Batteries for electric vehicles are defined by their relatively high power-to-weight ratio, specific energy, and energy density; smaller, lighter batteries are required because they reduce the weight of the vehicle. These factors improve its performance including range, acceleration, and deceleration. Compared to fossil-fuel-based vehicles that use petrol or diesel, most current battery technologies still have much lower specific energy. This negatively impacts the maximum driving range.
The most common battery type in modern electric vehicles is lithium-ion, because of its high energy density compared to its weight. The total amount of electric energy that can be stored in batteries is measured in kilowatt-hours (kWh). The average capacity is around 40kWh, but some cars now have up to a 100kWh capacity. The battery capacity of your car will have a direct impact on its range. That's the number of miles you can drive on a full charge. The higher the kWh, the better. In terms of mass-produced batteries, lithium-ion batteries are the ones with the highest energy density. Lithium-ion batteries' energy density can typically range between 100 to 270 Wh/kg, while lead-acid batteries range from 5 to 50 Wh/kg. The following graph shows the relative benefits of lithium-ion batteries compared to other chemistries for the EV sector, demonstrating high power density and high energy density:
Source: Creative Commons CC0 1.0 Universal Public Domain Dedication.
What is Lithium Ion battery chemistry?
We will focus on lithium-ion batteries most current battery technologies, which are split into Nickel-Manganese-Cobalt ("NMC") and Lithium-Iron-Phosphate ("LFP") types of which the former is the more popular amongst EV car manufacturers. When referring to these two chemistries, this is the material for the cathode. The material for the anode is usually graphite and the electrolyte are various types of lithium salt. Based only on the cathode material the following diagram illustrates the difference in typical composition between NMC and LFP batteries:
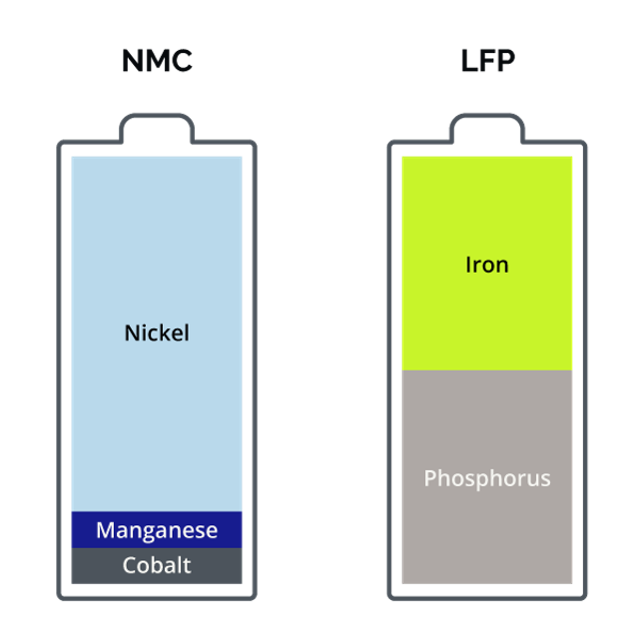
The above are only the cathodes. Graphite will be needed for the anode and lithium salts for the electrolyte. Therefore, the main minerals required for the manufacture of these types of EV batteries are:
NMC: Primarily Nickel, lithium, and graphite
LFP: Primarily Phosphorus (i.e. phosphate), iron, lithium, and graphite
There are relative costs and benefits between the two types:
- Energy density: NMC has higher energy density than LFP
- Range: NMC has more range than LFP
- Cost of materials: LFP is cheaper than NMC
- Environmental cost: LFP does not need nickel so has a lower environmental cost than NMC
- Fire risk (i.e. safety): LFP lower risk than NMC
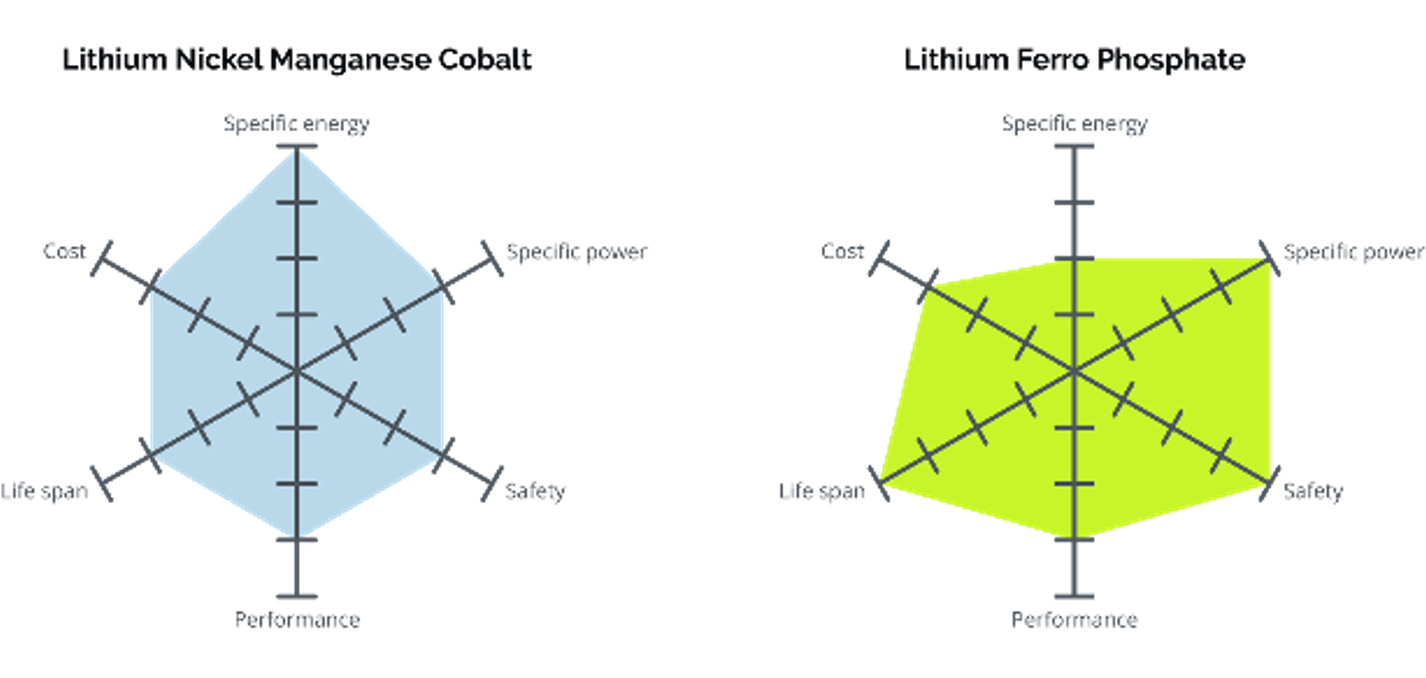
Supply of Minerals Required for EV batteries
As NMC batteries currently dominate the market share of lithium-ion EVBs. In this article, we will focus on the three minerals identified above that dominate the chemistry of NMC batteries which: lithium, nickel, and graphite.
LITHIUM
The lithium required for EVBs can be obtained from two main sources: hard rock ore mining and the extraction of lithium-rich brines from salt deserts. The main countries producing lithium from hard rock sources are Australia, China, and Zimbabwe. Extraction of lithium brines from salt deserts occurs mainly in South America, in particular Argentina and Chile.
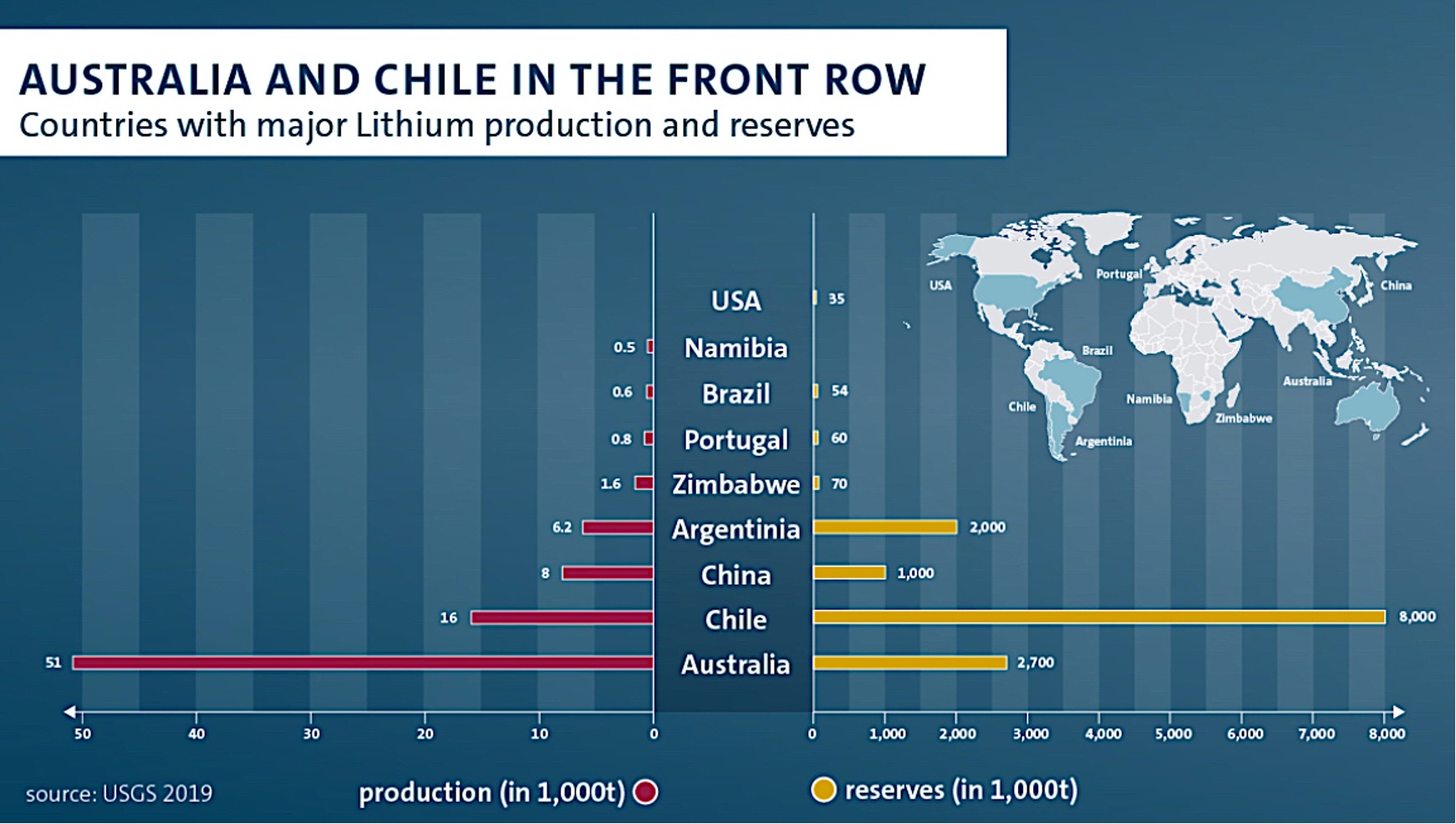
Production has been increasing rapidly in recent years as the adoption of EVs globally increases.
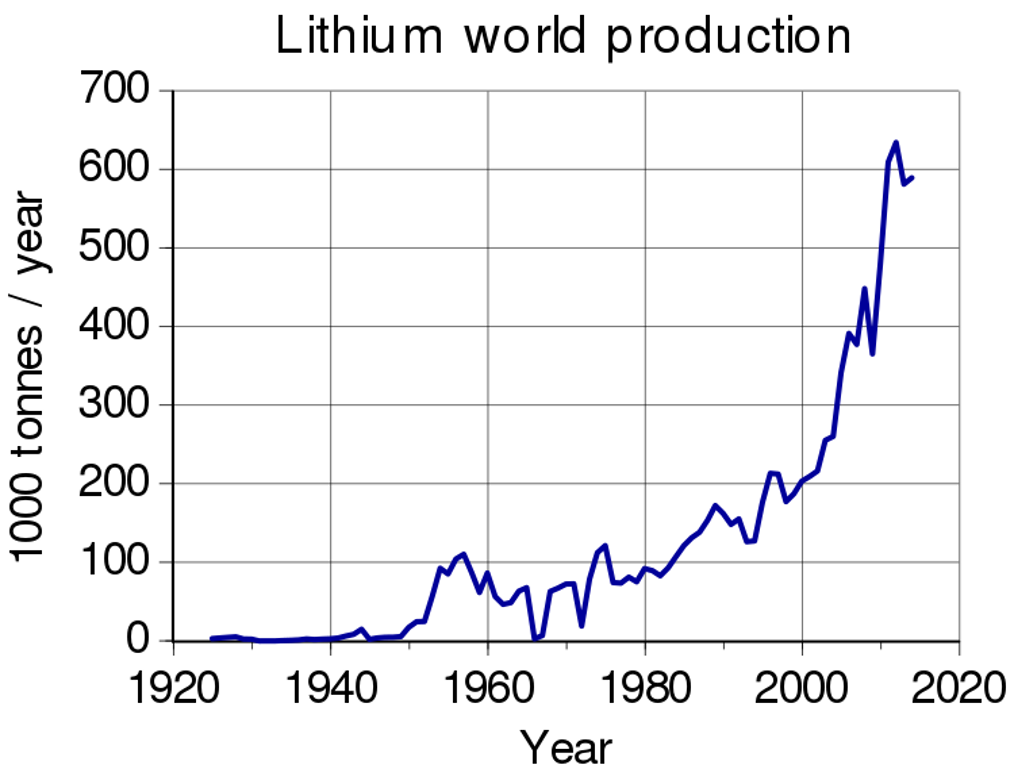
Most commercial lithium production is from those that extract lithium from underground brine reservoirs called "salars" in South America. Much of this takes place in the so-called "Lithium Triangle" at high altitude in the Andes mountain range, where the borders of Bolivia, Argentina, and Chile meet, as well as some in China. Lithium brine recovery is a straightforward but time-consuming process because lithium-rich water is pumped to the surface and into a series of evaporation ponds which takes several months to evaporate and leave salts with lithium precipitating out. The following photo shows an aerial view of Salar de Olaroz Lithium Mine, Argentina.
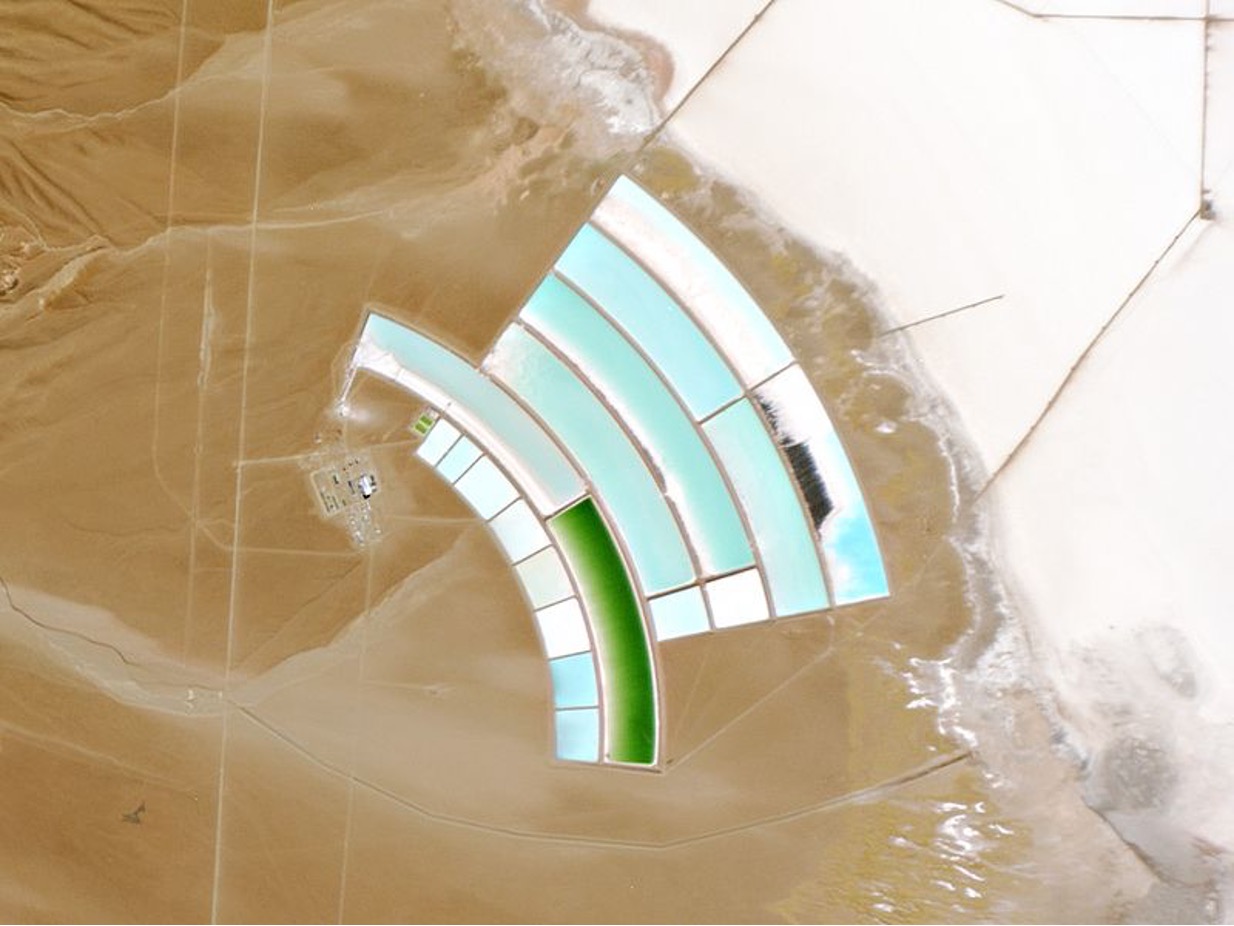
Hard rock mining is a more geologically complex and energy-intensive process than conventional brine extraction, although the process is not as time-consuming. Three main lithium-rich minerals are used for commercial lithium extraction which are spodumene, lepidolite, and petalite. Spodumene is the most common. Australia accounts for much of the world's spodumene production. The photograph below shows an example of lithium-containing spodumene rock.
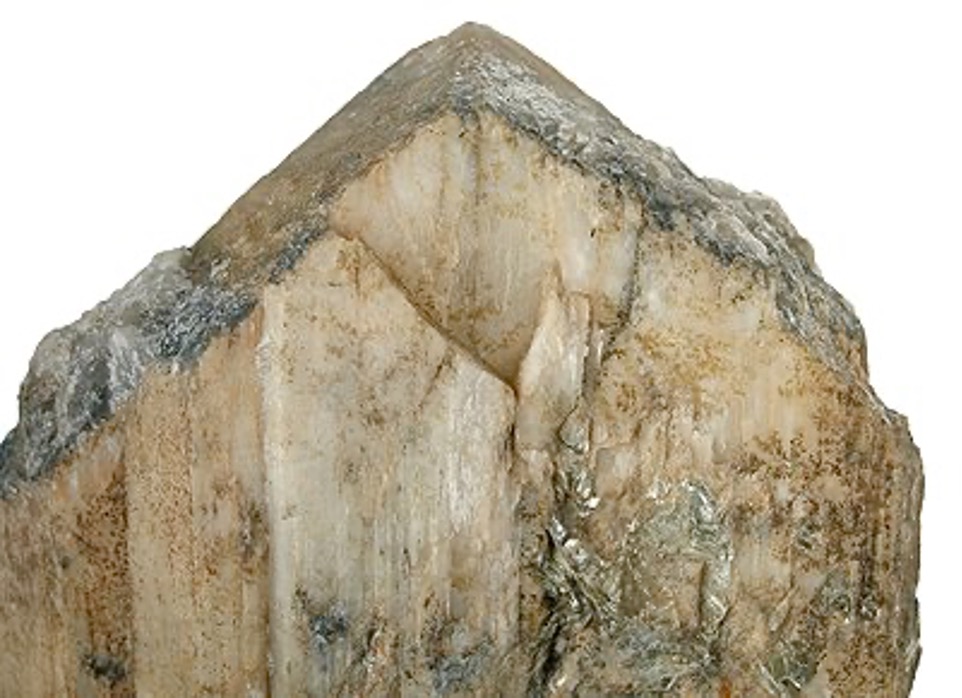
NICKEL
Nickel is considered a "minor metal" that is mainly used as an additive to steel to produce stainless steel to improve strength and corrosion resistance. The price of nickel is controlled by the demand for stainless steel. This remains the dominant use of nickel, with nickel for EVBs currently not a significant source of demand, as visualized in the next graphic.
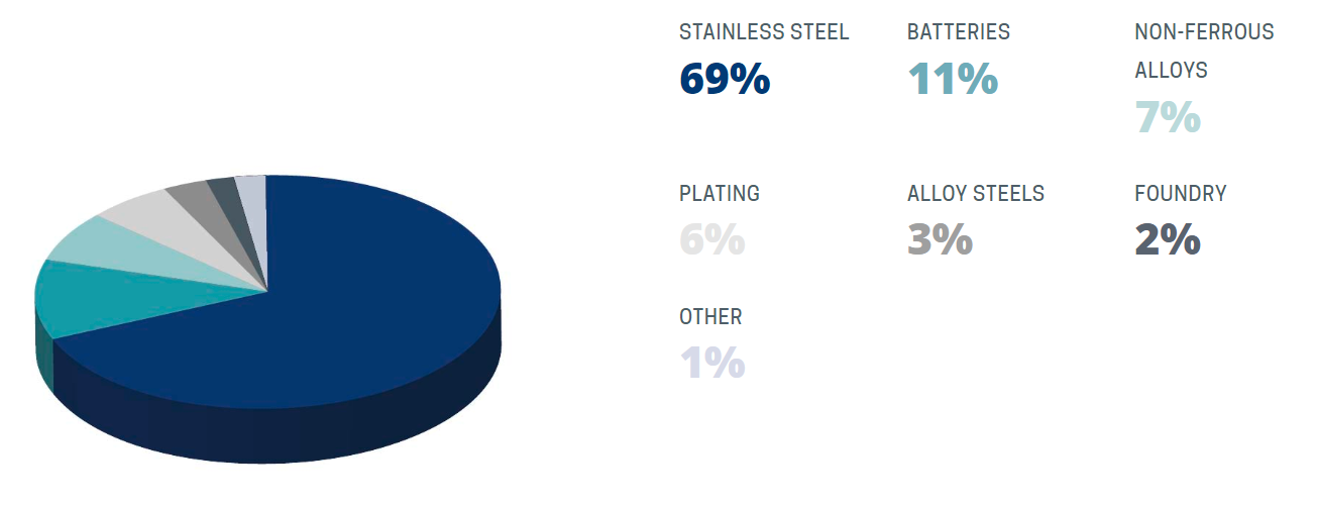
The growth of the demand for the battery segment is expected to be significant as illustrated below. The demand from the battery sector will have a more significant influence on the nickel price in the future, with demand for nickel expected to almost double by 2040 primarily due to growth in use in EVBs:
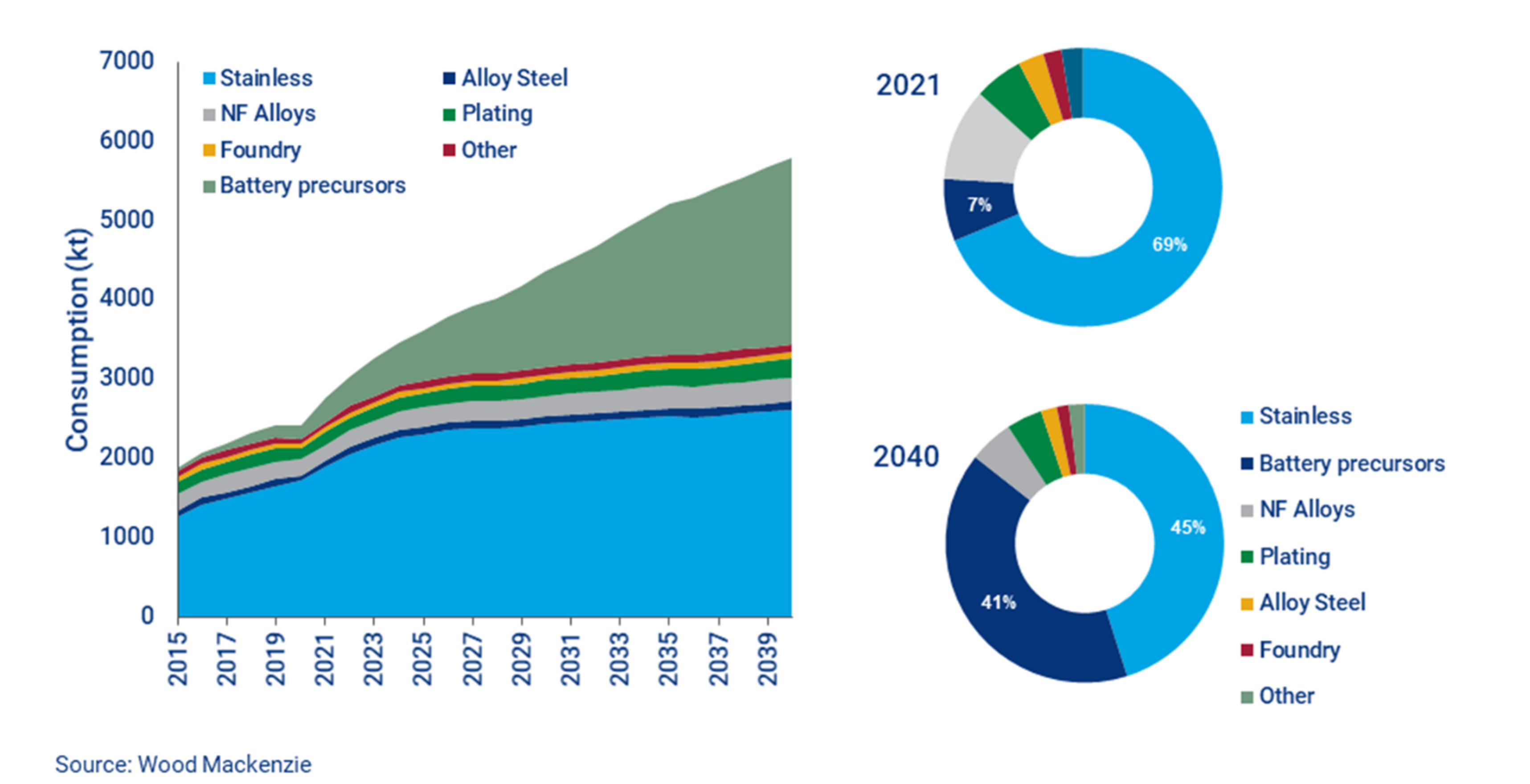
In terms of mine supply, there are two main types of ore from which nickel is extracted. Nickel sulfide deposits are typically deep underground and more expensive to mine in comparison to laterite deposits, which are found at the surface and can be open-pit mined. Additionally, sulfides are typically a higher grade than laterites. However, sulfide ores are easier and cheaper to process than laterites. Sulfides are found deep in the earth's crust and are much harder and costlier to find. Sulfide ore is mainly used to produce nickel for EV batteries, whereas laterite ores mainly feed the stainless steel industry.
GRAPHITE
For lithium-ion EVB anodes, graphite is the dominant material preferred by EVB manufacturers. There are two sources for such graphite: natural (flake) graphite and synthetic.
Natural flake graphite is directly mined from ore deposits, whereas synthetic graphite is made using petroleum as a feedstock. Natural graphite has a cost advantage relative to synthetic graphite, with natural graphite roughly half the cost of synthetic graphite. Synthetic graphite, however, is costly, power intensive, and environmentally unfriendly, with supply dominated by China, which contradicts EV manufacturers' desire for a more localized supply chain of ESG responsibility. Natural graphite lags behind synthetic graphite in the key area of lithium-ion EVB performance and consistency. Synthetic graphite is still favored by lithium-ion EVB manufacturers for its consistency and performance. Synthetic graphite still dominates the anode supply chain. Made from coke or "pet coke" (the carbon that's left over from oil and coal refining) it is heated to a very high temperature of over 2500°C which is a highly energy-intensive process, with high CO₂ emissions.
Most graphite production currently comes from China, as indicated by the following pie chart:
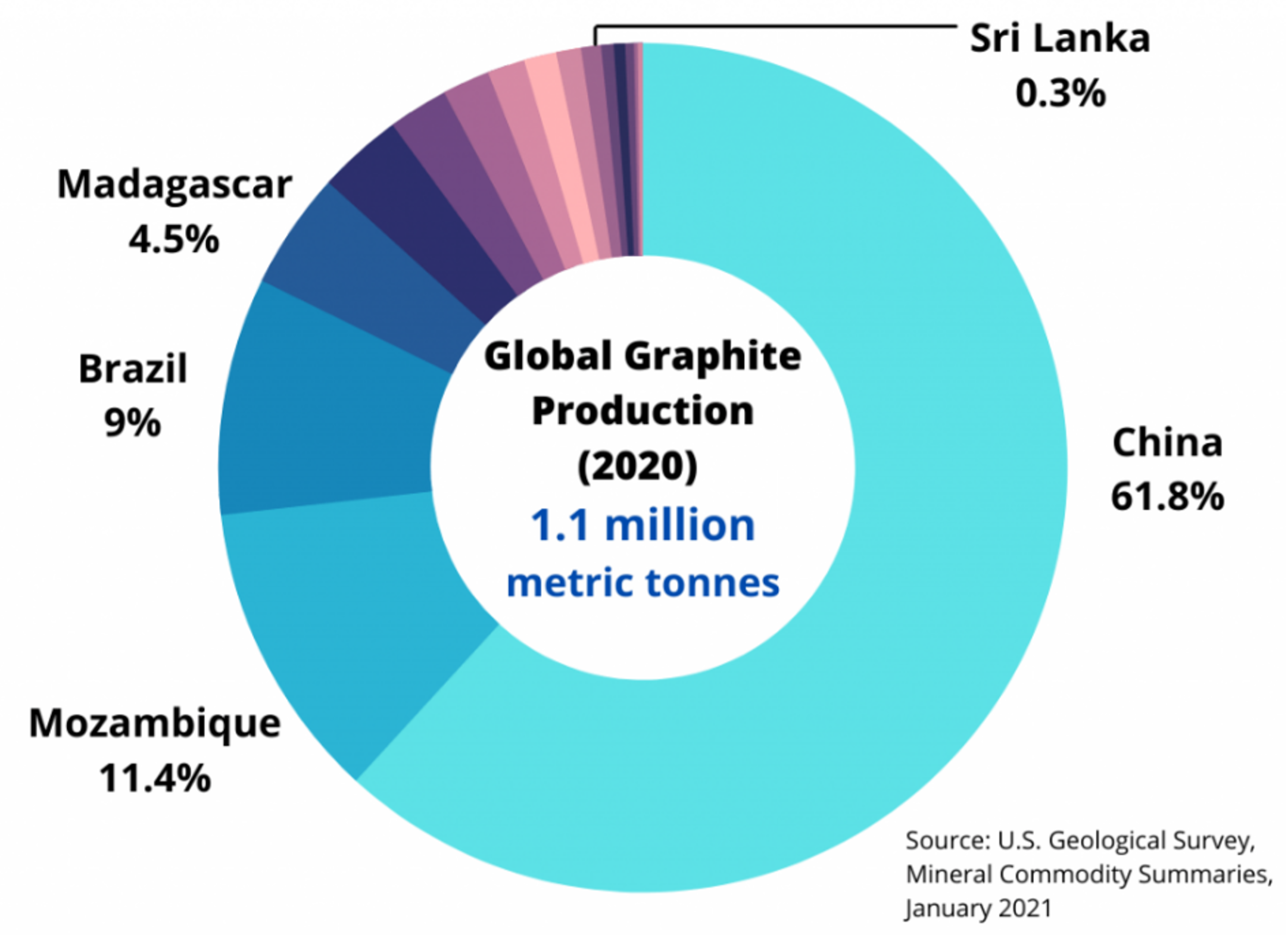
Graphite makes up the majority of the anode (95%) of a typical lithium-ion EVB meaning that about 1kg of graphite is needed per kWh of battery energy making it the most significant element of the battery cell in terms of weight. China has reached a position of dominance in the supply of the type of high-grade processed graphite needed for lithium-ion EVBs. There is a desire in the West for new sources of graphite, in particular natural flake graphite from Africa and Australia.
Therefore, there is now tremendous attention towards investment into new natural graphite mines in Africa, Australia, and Canada which can mine low-cost natural graphite and convert it via processing to a higher-performance version that can match the quality of synthetic graphite in lithium-ion EVB applications.